There are 5 levels of injection mould maintenance:
level 1. Routine Maintenance
Before the mold is removed from the press, it is to be heated so that all surface condensation is evaporated. With the 20L Bucket Mould still warm, internalmold surfaces should be gently cleaned with shop safety solvent to remove any residual dirt and grime, the ejector system moved fully forward, then sprayed with approved rust preventive before the ejector system is retracted and the mold closed. Lenses and highly polished surfaces should be protected following specificinstructions. All water lines should be drained and blown free of all residual water to avoid buildup of rust due to standing water. It is imperative that no water be trapped insidemold. Check and assure all bolts, plates, clamps etc. are in place and tight. Bag the last shot as an example of the typical quality of this run. Store these partswith the mold.
level 2. Simple Preventive Maintenance
Open the mold. Using properly approved safety shop solvent, remove the mold preservative with a lint free pad. It is bad practice to immediately run parts on the assumption that the first shots will scrape away the protective coating and will therefore be used to clean out the mold preservative.
level 3. Inspection Maintenance
This maintenance is performed by the lead operator or a tool maker at the end of aproduction run. Using the check list and visual inspection techniques, the mold is looked over and any minor repairs that are necessary are noted for the convenienceof the General Maintenance procedure. If not, needed repairs or future required touch up notations are kept with the mold history log for future evaluation. Any components missing or cavity blocked off should be noted and attended to. A sample from the blocked cavity should be retained for the mold maker to make repairs. The mold should be washed with safety solvent to remove the varnish and build upfrom the molding process. The vents should be checked for depth in a minimum of four clockface places aroundthe cavity face. Notations for work to be done during the General Maintenance procedure should be noted on the form for future work Bent, worn or broken ejector pins should be noted. The mold should be removed from production and the pins replaced.
Level 4. General Maintenance
Only competently trained tool room technicians should perform this maintenance. All plates are separated and their faces cleaned. Caution: Highly polished surfaces should not be cleaned with brushes or rags. Use only uncontaminated facial tissues or cotton balls. Loosen dirt by spraying cleaning fluid into cavity and wipe clean with clean cotton balls. Do not touch with fingers, dust on fingertips may scratch apolished surface. Be careful when blowing a cavity out, there may be dust or rust in the air lines which may damage the polished cavity. All components are checked for wear. Any excessive wear is noted and a determination is made to repair, replace or continue to use. All rough areas outside the cavity detail area are to be worked out. Any area insidethe cavity detail area with dings, dents or other signs of wear or abuse should beconsidered critical and should be carefully analyzed before replacements or repairs are commenced. All moving parts are to be lubricated if required. Use lubricant sparingly on all moving parts which make contact with plastic partsVents should be checked for depth, width and land as compared to the tool drawing specifications. This data should be recorded on the check list and a determinationmade to repair if required. They should also be checked for corrosion and vent burns “O” rings, seals and gaskets should be checked for integrity. All water lines are to be pressure tested for leaks and recertified for flow capacity.Water lines that have built up scale and are restricted should be pressure cleanedwith a descaling agent. The ejector system is to be examined for proper alignment. If the ejector pin holes have become egg shaped it must be determined if they should be redrilled and bored to a larger size and the existing pins replaced with over size pins. Broken return springs, replating or retexturing as a result of the material eroding the 18L Bucket Mouldsurface, replacement of gates or gate inserts, new runner blocks etc. must be analyzed and determined. Replace all springs after 50,000 cycles. https://www.rixiangmould.com/
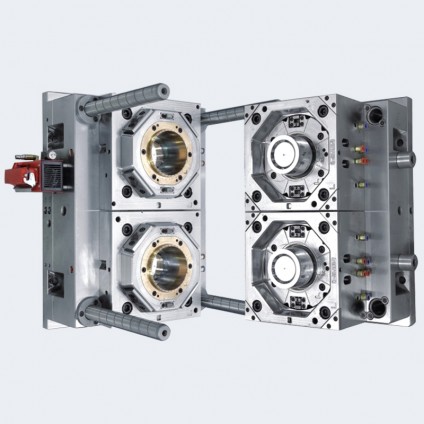